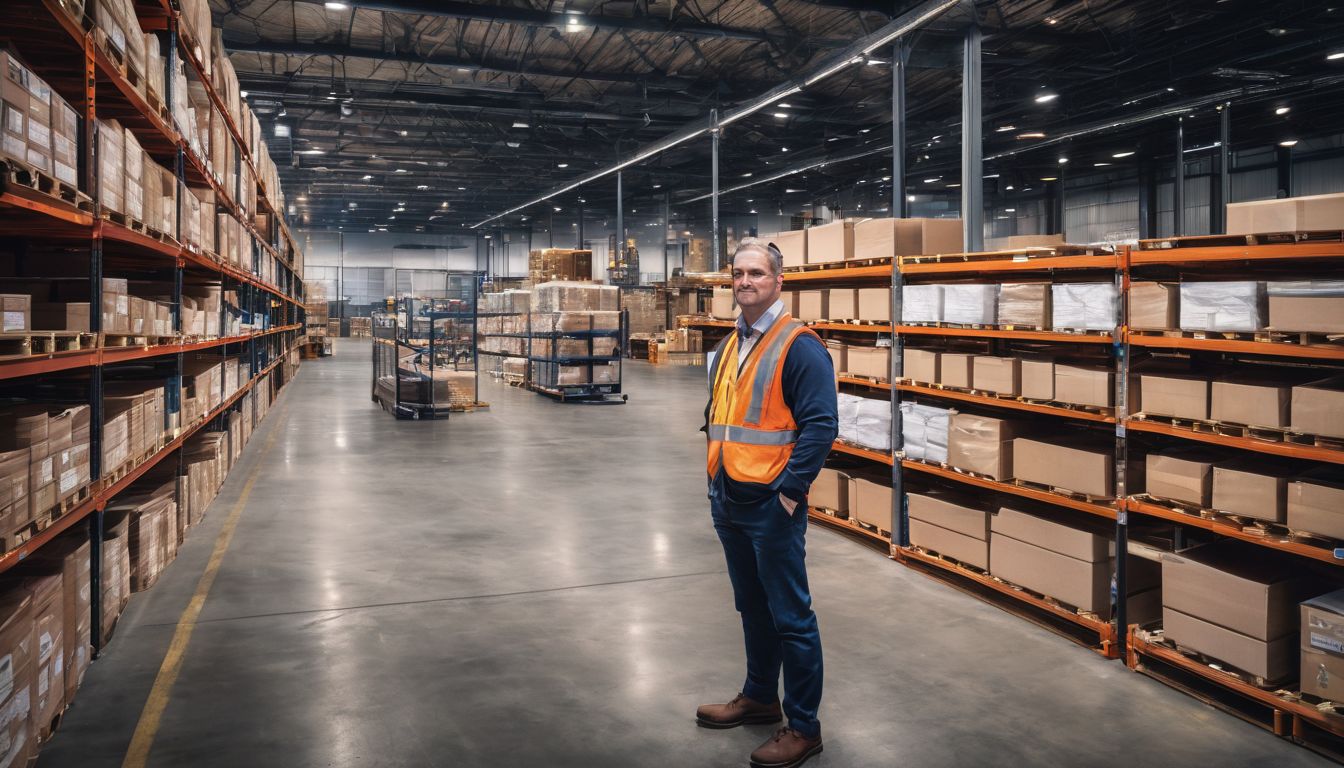
Understanding Multi-Location Inventory Management
Multi-location inventory management is key for businesses with more than one facility. Think of a company that makes products in two factories. Or it may keep items in many warehouses around the world.
All these places need to work together as part of the whole business.
To do this well, companies use special software like Easy WMS or Deskera ERP to track and guide their stock. The software keeps an eye on all goods moving in and out across different spots.
This way, orders can be filled from any place that has the right item ready.
With good multi-location inventory management, a business knows what it has and where every bit is located at any time.
3 Big Challenges of Multi-Location Inventory Management
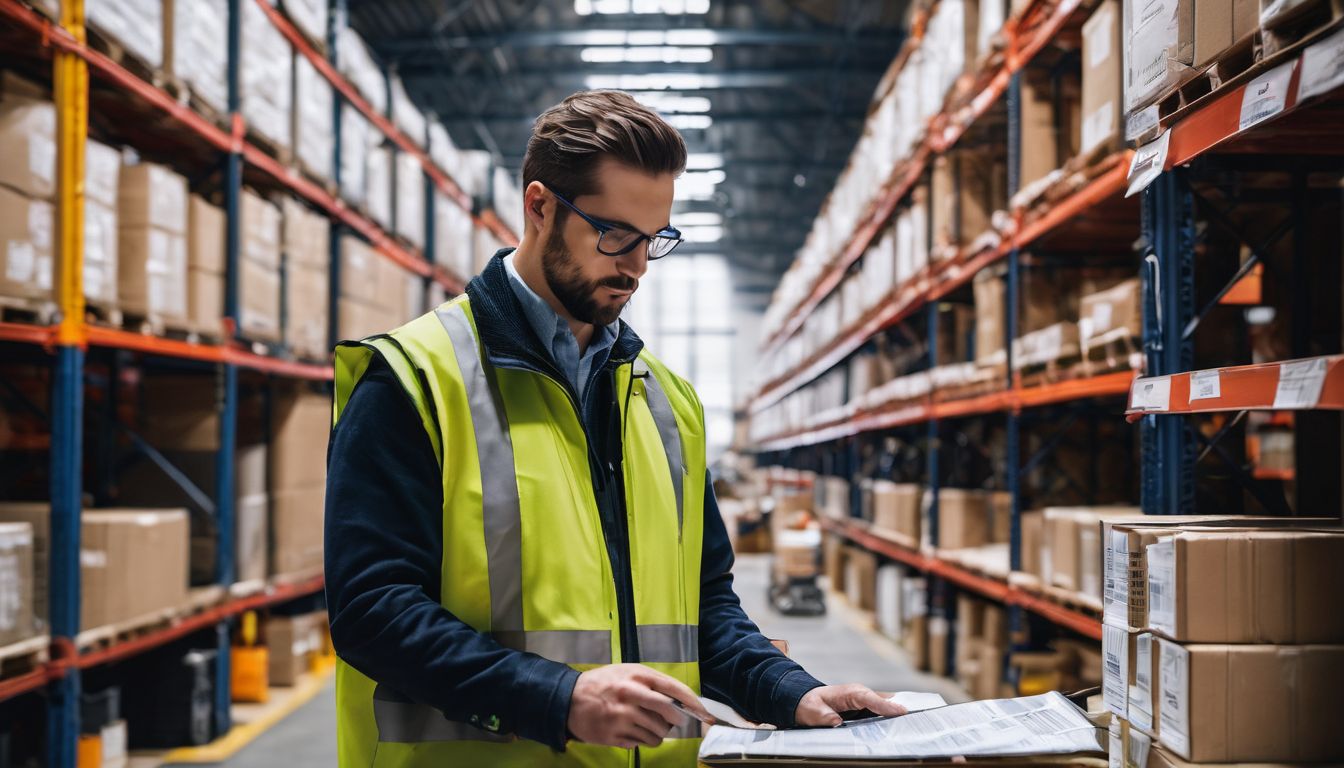
Multi-location inventory management presents several challenges, including difficulty in communication, inconsistent inventory standards, and lack of a centralized, synchronized system.
1. Difficulty in communication
Talking with different places can be hard. In multi-location inventory management, this is a big problem. This problem can slow down the supply chain and make work difficult. For example, warehouse A might not know what warehouse B is doing.
This can lead to many problems like delays or mix-ups in orders.
The Easy WMS system by Interlake Mecalux can help solve these problems. It makes it easy for all the warehouses to talk to each other. With good communication, there will be fewer mistakes and faster work.
2. Inconsistent inventory standards
Inconsistent inventory standards can cause problems. Not all places count or track items the same way. One spot might use a barcode system while another uses manual methods. This mix-up makes it hard to know where things are and how many you have.
The use of multi-location inventory management software helps fix this issue. It watches all item movement in different spots, from getting new items to sending out orders. All sites must follow the same rules for counting and checking stock with this system in place.
3. Lack of a centralized, synchronized system
A key issue in managing stock at many places is the lack of a linked system. This can lead to wrong counts of goods. It also makes it hard to keep an eye on and handle items stored in different places.
A single system that links all locations would solve this problem.
Without a tied-together system, talking between teams at different sites becomes harder too. This can make keeping the warehouse neat more complex. Meeting rules set by others also gets tougher without such a system.
6 Advantages of Multi-Location Inventory Management
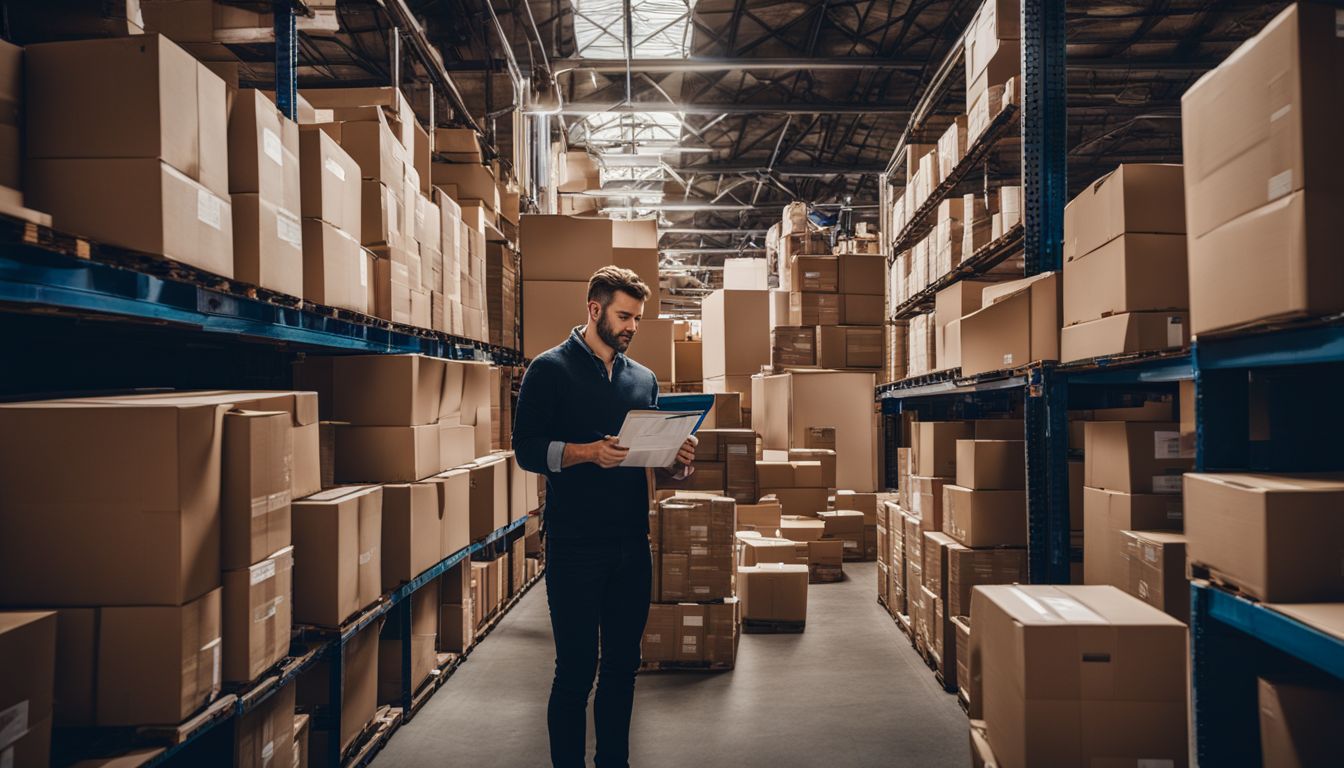
Improved communication. Rapid deliveries. Lowered costs. Increased customer satisfaction. Flexible inventory control. Reduction of carbon footprint. These are just a few of the advantages that multi-location inventory management can bring to your business.
Discover how you can master the art of managing inventory across multiple locations by reading on!
1. Improved Communication
Effective communication is essential in multi-location inventory management. When there is improved communication between different locations, it becomes easier to coordinate and manage inventory across the entire supply chain.
This leads to better visibility and understanding of inventory levels, ensuring that products are available when and where they are needed. Improved communication also allows for more efficient collaboration between teams, reducing errors and delays in order fulfillment processes.
With effective communication channels in place, decision-making becomes faster and more accurate, leading to smoother operations and increased customer satisfaction. In fact, studies have shown that businesses with strong internal communication systems experience higher productivity levels and greater overall success.
2. Rapid Deliveries
Multi-location inventory management plays a crucial role in facilitating rapid deliveries. By having multiple locations strategically placed, businesses can ensure that products are closer to their customers, reducing travel distances and enabling faster order fulfillment.
Micro-fulfillment centers located in key areas can further expedite the delivery process by bringing inventory even closer to the end consumer. This not only improves customer satisfaction but also helps businesses meet the increasing demand for quick and efficient deliveries.
Efficient multi-location inventory management software allows businesses to track inventory in real-time, ensuring that orders can be processed and shipped promptly, contributing to speedy deliveries.
3. Lowered Costs
One advantage of multi-location inventory management is that it can help reduce costs. By having multiple warehouses strategically located, businesses can minimize transportation expenses and shorten delivery times.
They can also take advantage of bulk purchasing and negotiate better deals with suppliers. With improved visibility and control over inventory, companies can avoid overstocking or stockouts, which can both lead to financial losses.
Additionally, by optimizing warehouse layouts and implementing efficient tracking systems, businesses can streamline their operations and reduce labor costs. Lowered costs in inventory management contribute to increased profitability and business success.
4. Increased Customer Satisfaction
Having multiple warehouses and implementing efficient multi-location inventory management strategies can greatly contribute to increased customer satisfaction. By having warehouses strategically located in different regions, companies can ensure faster deliveries and streamline product distribution.
This leads to shorter fulfillment times and improved overall customer experience. Additionally, with a synchronized inventory management system like Easy WMS software, businesses can accurately track their stock levels across all locations, avoiding stockouts and ensuring prompt order fulfillment.
This level of visibility and control enhances customer satisfaction by reducing the likelihood of delayed or incomplete shipments. Furthermore, by optimizing warehouse layout and implementing flexible inventory control practices, companies can better meet customer demands while minimizing errors or discrepancies in order processing.
5. Flexible Inventory Control
Flexible inventory control is a crucial aspect of multi-location inventory management. With the help of inventory management software like Easy WMS, businesses can have better control over their inventory across different locations.
This software allows for efficient optimization of tasks in each facility, ensuring that inventory is properly managed and distributed. Easy WMS tracks all movements within warehouses, including inflows and order processing.
It also facilitates goods transfers between warehouses, making sure that the right products are in the right place at the right time. Implementing Easy WMS through the SaaS model provides easy accessibility from anywhere with an internet connection, giving businesses the flexibility they need to manage their inventory effectively.
6. Reduction of Carbon Footprint
Multi-location inventory management plays a crucial role in reducing businesses' carbon footprint. By optimizing inventory and strategically locating stock based on demand, companies can minimize travel distances for delivering orders.
This means fewer fuel emissions and less impact on the environment. For example, logistics provider Casintra and motorcycle manufacturer SHAD both use Easy WMS from Interlake Mecalux to coordinate their facilities in different locations, potentially reducing their carbon footprint.
By efficiently managing inventory across multiple sites, businesses can contribute to sustainability efforts while maintaining smooth operations.
Best Practices and Strategies for Multi-Location Inventory Management
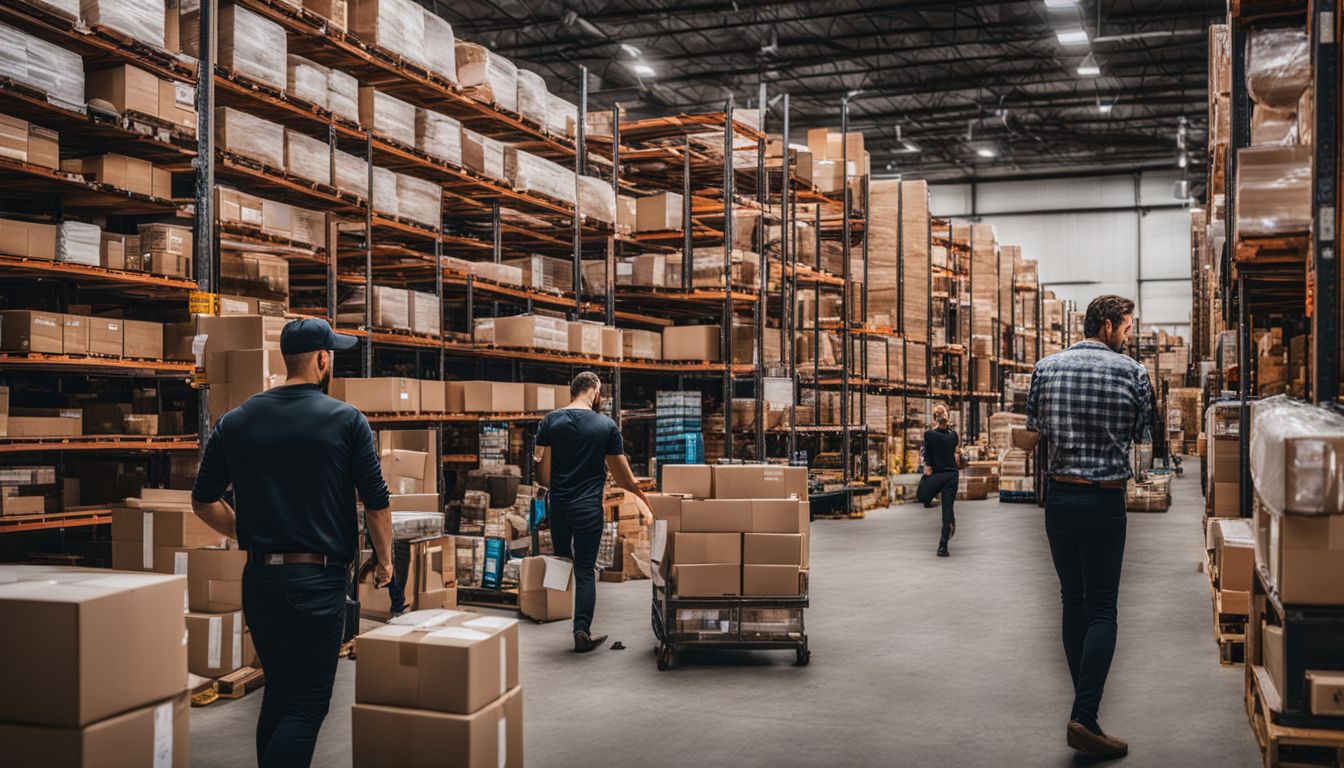
Implement an Efficient Tracking System, manage supply chain costs, keep accurate records, manage inventory in real-time, optimize warehouse layout, and set up safety stock.
Implementing an Efficient Tracking System
Implementing an efficient tracking system is crucial for effective multi-location inventory management. With such a system in place, businesses can easily track and monitor their inventory across different locations in real-time.
This enables them to have accurate visibility into stock levels, reduce the chances of stockouts or overstocking, and make informed decisions about purchasing and replenishment. An efficient tracking system also improves communication between warehouse teams and reduces errors by automating data entry and providing up-to-date information on product movement.
Overall, implementing an efficient tracking system streamlines operations, increases efficiency, and enhances customer satisfaction.
Managing Supply Chain Costs
Managing supply chain costs is crucial for businesses to improve profitability and maintain customer satisfaction. Here are some strategies to effectively manage supply chain costs:
- Analyze and optimize transportation expenses: Evaluate transportation routes, modes, and carriers to identify cost-saving opportunities. Consolidate shipments, negotiate better rates with carriers, and use technology solutions for route optimization.
- Optimize inventory levels: Analyze demand patterns, lead times, and order frequencies to determine optimal inventory levels. By avoiding excess stock and minimizing stockouts, you can reduce holding costs and improve cash flow.
- Use data analytics for demand forecasting: Leverage historical sales data, market trends, and customer insights to forecast demand accurately. This helps in aligning production schedules with actual demand, reducing inventory carrying costs, and preventing overproduction.
- Collaborate with suppliers: Build strong relationships with suppliers to negotiate favorable pricing terms and secure volume discounts. Explore opportunities for joint planning and sharing of demand forecasts to optimize inventory management throughout the supply chain.
- Implement lean manufacturing principles: Identify waste within the production process and eliminate non-value-added activities. Adopting lean manufacturing practices helps in reducing production time, material waste, energy consumption, and overall operating costs.
- Automate processes through technology: Invest in supply chain management software that streamlines operations, improves visibility across the entire supply chain network, automates repetitive tasks, reduces errors, and maximizes efficiency.
Keeping Accurate Records
Keeping accurate records is crucial in multi-location inventory management. It helps ensure that all inventory information is up-to-date and reliable, enabling efficient decision-making.
With the help of multi-location inventory management software like Easy WMS from Interlake Mecalux, businesses can track and record all movement and transactions across their various facilities.
This includes inflows, order processing, distribution, and goods transfers between warehouses. By maintaining accurate records, businesses can prevent errors, identify bottlenecks or discrepancies in real-time, and optimize their overall inventory management process for improved efficiency and profitability.
Managing Inventory in Real-Time
Managing inventory in real-time is crucial for businesses that operate in multiple locations. With the help of multi-location inventory management software, such as Easy WMS from Interlake Mecalux, businesses can monitor their inventory movements across various facilities in real-time.
This includes tracking incoming stock, processing orders, and distributing products efficiently. By having a centralized system that provides up-to-date information on inventory levels and locations, businesses can make quick decisions to optimize their supply chain and ensure that they have the right products available when customers need them.
Real-time inventory management also helps reduce the risk of stockouts or overstocking, improving overall operational efficiency and customer satisfaction.
Optimizing Warehouse Layout
Optimizing warehouse layout is a crucial aspect of effective multi-location inventory management. By strategically organizing the layout, businesses can maximize their storage capacity and enhance operational efficiency.
Factors such as customer demand, shipping costs, and order fulfillment timelines should be considered when determining the most efficient placement of products within the warehouse.
Implementing efficient storage and picking strategies can help improve inventory control and reduce order bottlenecks. Analyzing unique needs and continuously evaluating warehouse layout can lead to streamlined operations and improved overall performance in multi-location inventory management.
Setting up Safety Stock
Setting up safety stock is a crucial step in multi-location inventory management. Safety stock refers to the extra inventory that is held as a buffer to mitigate unexpected fluctuations in demand or supply.
By having safety stock, businesses can ensure that they have enough inventory on hand to fulfill customer orders even during unforeseen circumstances like supplier delays or sudden spikes in demand.
Setting up safety stock involves determining the appropriate quantity of inventory to hold based on factors such as lead time, demand variability, and desired service levels. It's important to strike a balance between having enough safety stock to meet customer demands and minimizing the costs associated with holding excess inventory.
Having safety stock helps minimize disruptions in the supply chain by reducing the risk of running out of popular items or key components. It provides a cushion against uncertainties and allows businesses to maintain continuity in their operations even during challenging times.
How Multi-Location Inventory Management Software Can Assist You
Multi-location inventory management software can be a valuable tool for businesses with multiple warehouses or facilities. This software helps synchronize inventory management across all locations, making it easier to track and manage inventory levels.
With this software, you can monitor all movements in various facilities and optimize tasks in each warehouse. It also supervises the transfer of goods between warehouses, ensuring that inventory is distributed efficiently.
Implementing multi-location inventory management software through the Software as a Service (SaaS) model is a popular choice for many businesses.
Casintra and SHAD are examples of companies that use Easy WMS, a type of multi-location inventory management software, to organize and coordinate their operations across multiple warehouses.
By utilizing this software, they are able to streamline their processes and ensure smooth operations across all their locations.
One major benefit of having multiple warehouses is the ability to provide faster deliveries to customers. With multi-location inventory management software in place, businesses can easily track stock levels at each location and fulfill orders from the nearest facility.
This reduces shipping time and improves customer satisfaction.
In summary, multi-location inventory management software offers several advantages for businesses with multiple facilities. It helps synchronize inventory across all locations, optimize tasks within each warehouse, supervise goods transfers between facilities, and facilitate faster deliveries.
Implementing this type of software can greatly improve efficiency and customer satisfaction while streamlining operations across different locations.
Conclusion
Mastering multi-location inventory management is crucial for businesses that operate in multiple facilities. By implementing best practices and strategies such as efficient tracking systems, managing supply chain costs, and optimizing warehouse layouts, businesses can effectively manage their inventory across different locations.
In addition, using multi-location inventory management software like Easy WMS from Interlake Mecalux provides centralized control and real-time visibility to streamline operations and enhance customer satisfaction.
With the right tools and techniques, businesses can overcome the challenges of multi-location inventory management and achieve success in their operations.
Key Takeaways
- Multi - location inventory management is essential for businesses with multiple facilities to ensure efficient stock control and order fulfillment.
- Challenges in multi - location inventory management include difficulty in communication, inconsistent inventory standards, and lack of a centralized system.
- Advantages of multi - location inventory management include improved communication, rapid deliveries, lowered costs, increased customer satisfaction, flexible inventory control, and reduction of carbon footprint.
- Best practices for multi-location inventory management include implementing an efficient tracking system, managing supply chain costs, keeping accurate records, managing inventory in real-time, optimizing warehouse layout, and setting up safety stock.
FAQs
1. What is multi-location inventory management?
Multi-location inventory management is a key part of supply chain analytics software. It helps businesses track and manage stock in different warehouses for speedier deliveries.
2. How can I lower costs with multi-location inventory management?
Using warehouse solutions such as pallet racks, automated storage systems AS/RS, and warehouse slotting software can help you cut costs by optimizing your storage space and improving the manufacturing process.
3. How does a Warehouse Management System (WMS) aid in managing inventory?
A WMS like Easy WMS from Mecalux offers easy modules and functionalities for better warehouse organization & design. It also gives detailed reports on SKUs through a custom dashboard to enhance customer training and professional services.
4.What improvements can be made with an Advanced Warehouse Management system?
Advanced WMS's have benefits beyond just tracking products, they allow seamless interaction with external servers like Deskera CRM or ERP Systems for improved accounting operations including billing and invoicing.
5.How does multi-carrier shipping software support multi-location inventory management?
It supports by enhancing customer satisfaction through faster deliveries from the nearest retail outlet or warehouse location considering demand, thus creating more customer loyalty.
6.What are green logistics in terms of Industry 5.0 vs Industry 4.0?
Green logistics involves reducing carbon footprint through efficient practices under new industrial norms of Industry 5.0 where sustainable solutions outdo traditional methods seen in Industry 4.0 era; thus it aids business expansion while ensuring environmental sustainability.