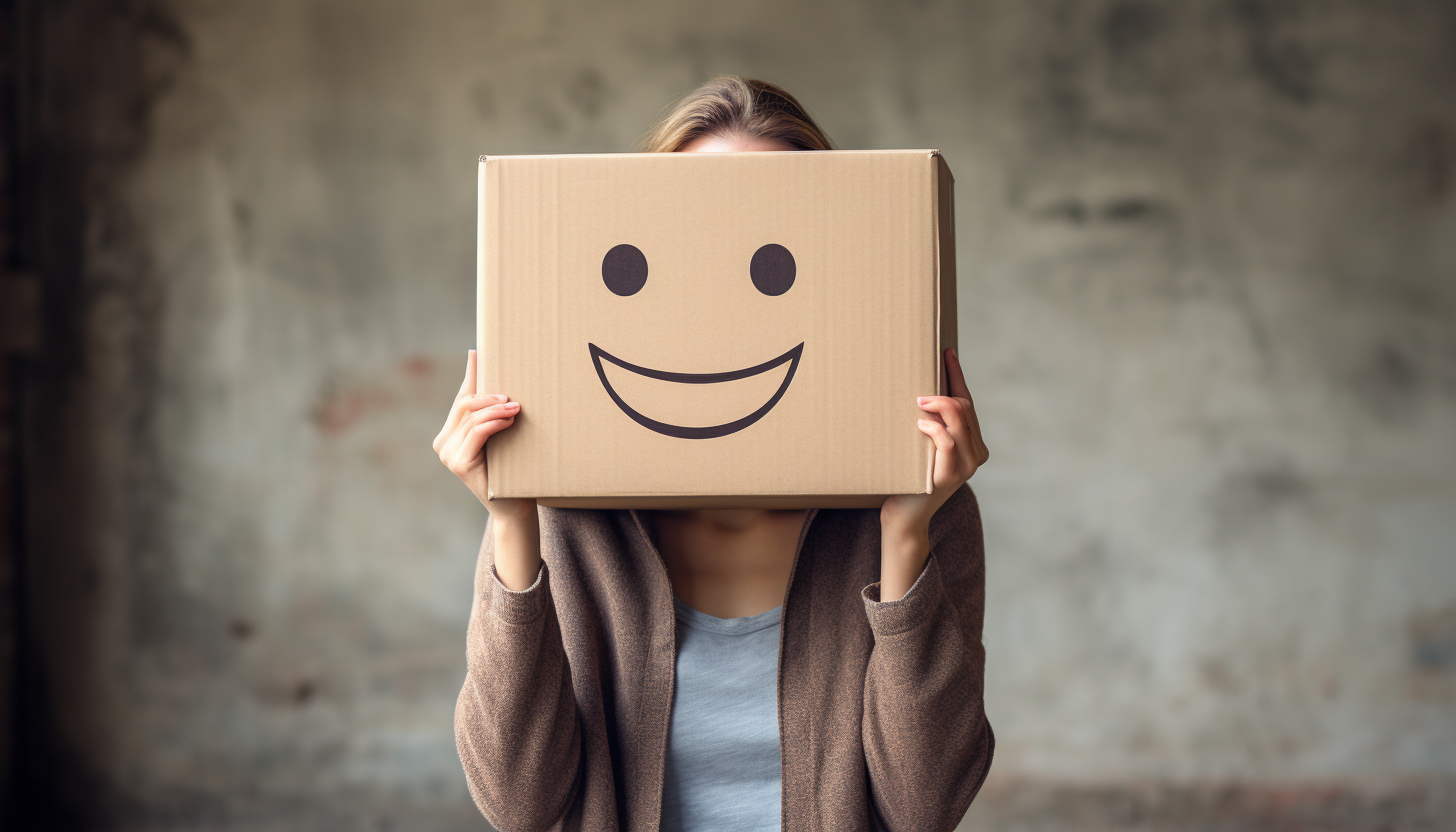
Understanding Minimum Stock Level
The Minimum stock level is a critical concept in ecommerce and inventory management. It refers to the lowest quantity of a particular product or item that a business should have in its inventory at any given time to ensure smooth operations and meet customer demand. Maintaining a minimum stock level helps prevent stockouts (running out of stock) and ensures that products are available for customers when they want to purchase them.
ELI5: Minimum stock level is the lowest amount of goods a store must have. It is good to know this number. This way, the store does not run out of things to sell. Keeping track helps avoid delays or no stock at all.
Calculating the minimum stock level involves considering factors such as demand variability, lead time, and desired service level. More on how to calculate minimum stock levels below!
Key Considerations for Establishing Minimum Stock Levels
Setting the minimum stock level for your inventory is a pivotal aspect of effective inventory management. It ensures that your business maintains a delicate equilibrium between satisfying customer demands and avoiding the costs associated with overstocking. To establish an optimal minimum stock level, here are some crucial factors to take into account:
- Calculate Average Daily Demand:Begin by calculating the average daily demand for each product in your inventory. This involves analyzing historical sales data over a relevant timeframe, such as a month or a quarter. Accurate demand forecasting is the cornerstone of determining how much stock you need to keep on hand to consistently meet customer needs.
- Incorporate Lead Time:It's essential to consider the lead time – the duration it takes for new shipments to arrive from your suppliers. Factor the lead time into your minimum stock calculation. This ensures that you replenish your inventory well in advance to prevent stockouts during the time it takes for new stock to arrive.
- Analyze Historical Sales Data:Delve into your historical sales data to uncover any trends or patterns that may influence your inventory levels. Identifying seasonal fluctuations or cyclical demand patterns will enable you to adjust your minimum stock levels accordingly. A thorough analysis of this data can be a game-changer in optimizing your inventory management strategy.
- Account for Supply Chain Variabilities:Supply chain disruptions and production delays can be unforeseeable yet impactful events. To safeguard against these uncertainties, consider adding a buffer stock to your minimum stock levels. This safety net helps ensure you don't run out of products during unexpected disruptions, maintaining your service levels and customer satisfaction.
- Continuous Monitoring and Adjustment:The business landscape is ever-evolving, with changes in market demand, competition, and customer preferences. Consequently, it's vital to regularly monitor and update your minimum stock levels. This proactive approach allows you to adapt to shifts in your industry, business growth, and evolving customer expectations.
- Leverage Inventory Management Systems:To streamline the process and enhance accuracy, consider utilizing an advanced inventory management system like SkuVault. Such systems automate the tracking of minimum stock levels and provide real-time insights into your inventory status. They can also generate alerts when it's time to reorder, taking much of the guesswork out of inventory management.
3 Important Reasons to Maintain Adequate Inventory Levels
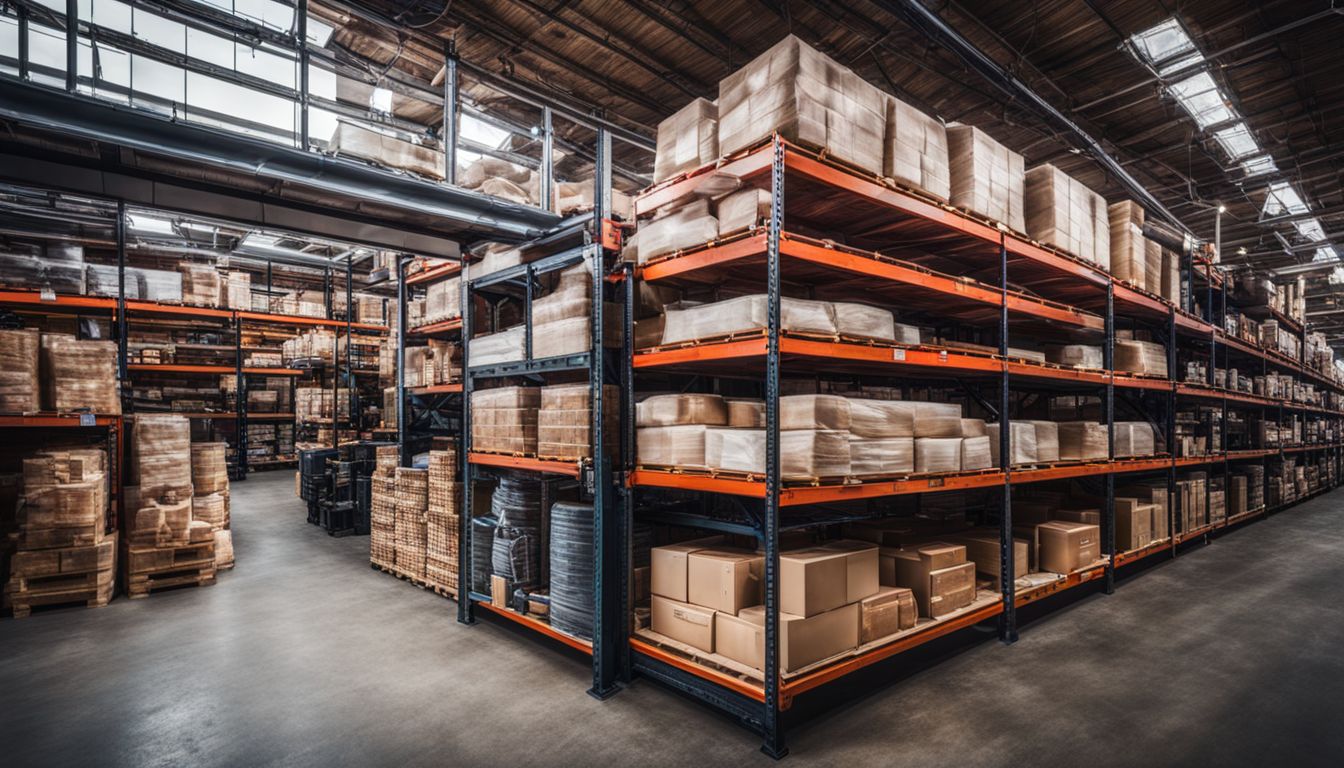
Maintaining adequate inventory levels is crucial for several reasons. It helps minimize missed sales, ensures wise cash investment, and enables early detection of any issues that may arise.
1. Fewer Missed Sales
Having enough items in your store means fewer missed sales. When customers can't find what they want, they go somewhere else. This hurts both sales and a brand's reputation. Maintaining the right stock levels helps to prevent this from happening.
By using methods like Average Demand or Safety Stock, you can find out the least amount of inventory needed. You don't just avoid missed sales, but also save money on storing too much stock.
2. Wise Cash Investment
Smart use of money matters in business. Buying too much stock eats up cash and space. But not having enough can lose sale chances and customers might go elsewhere. To avoid this, firms must keep an optimal level of inventory.
This is where calculating the minimum stock levels comes into play. It helps to save on storage costs and prevent lost sales due to stock outs. Tools like SkuVault help with this task by tracking your items and giving alerts when stocks are low or high based on set limits.
This way, businesses can get the most from their money while still meeting customer demand.
3. Early Detection of Issues
Spotting and solving problems early saves money. It stops you from running out of stock. It also keeps you from having too much stock, which costs money to store. Tools can help watch your stock levels so you spot these problems early.
Calculating your minimum inventory level is one way to do this. You might add safety stock to this level as well, just in case there are delays or a sudden jump in demand for your products.
How to Calculate Minimum Stock Levels
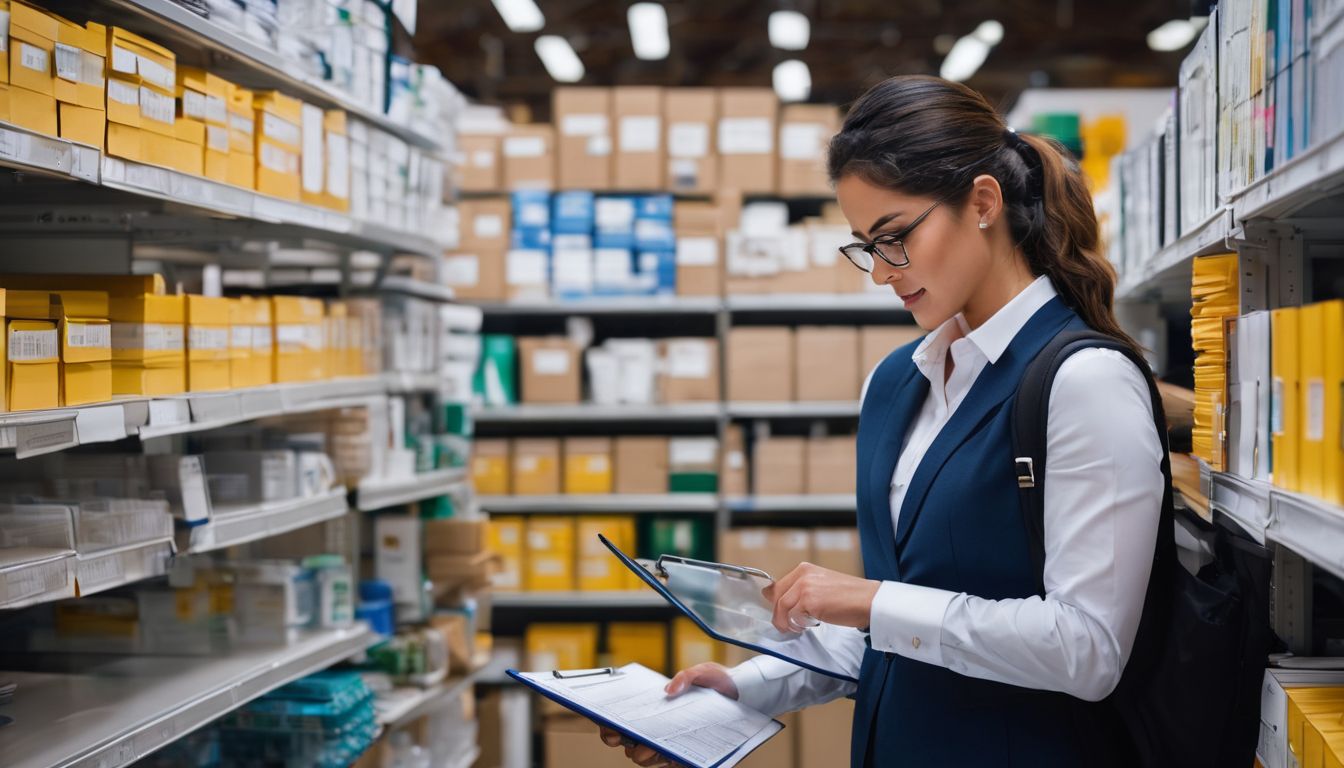
There are various methods to calculate it, but one common approach is to use the following formula:
Minimum Stock Level = (Reorder Point) + (Safety Stock)
Here's how to calculate each component:
1. Reorder Point (ROP):
The reorder point is the inventory level at which you should place a new order to replenish stock before it runs out during the lead time (the time it takes for the new inventory to arrive). The ROP is calculated as: ROP = (Average Daily Demand) x (Lead Time in Days)
2. Average Daily Demand:
This is the average number of units sold or used per day. You can calculate it using historical sales data over a relevant time period (e.g., a month).
3. Lead Time in Days:
The lead time is the time it takes for your supplier to deliver the goods after you place an order. It's essential to consider the lead time variability as well if it's not constant.
4. Safety Stock:
Safety stock is a buffer quantity of inventory that you maintain to account for uncertainties in demand and lead time. It ensures that you have enough stock to cover unexpected fluctuations. The safety stock is calculated based on factors like desired service level and demand variability. A common formula to calculate safety stock is:
Safety Stock = (Z-score for Desired Service Level) x (Standard Deviation of Demand during Lead Time)
5. Z-score for Desired Service Level:
This value is obtained from a standard normal distribution table and corresponds to your desired service level (e.g., 95% service level corresponds to a Z-score of approximately 1.65).
6. Standard Deviation of Demand during Lead Time:
Calculate the standard deviation of the daily demand during the lead time period.
Once you have calculated the ROP and Safety Stock, you can add them together to determine the Minimum Stock Level.
Minimum Stock Level = ROP + Safety Stock
It's important to note that the values used in these calculations should be based on historical data and adjusted as necessary to reflect changes in demand patterns and lead times over time. Additionally, different businesses may have varying approaches to setting their desired service levels and safety stock levels based on their risk tolerance and customer service goals. Therefore, the specific calculations may vary from one organization to another.
Benefits of Minimum Stock Level
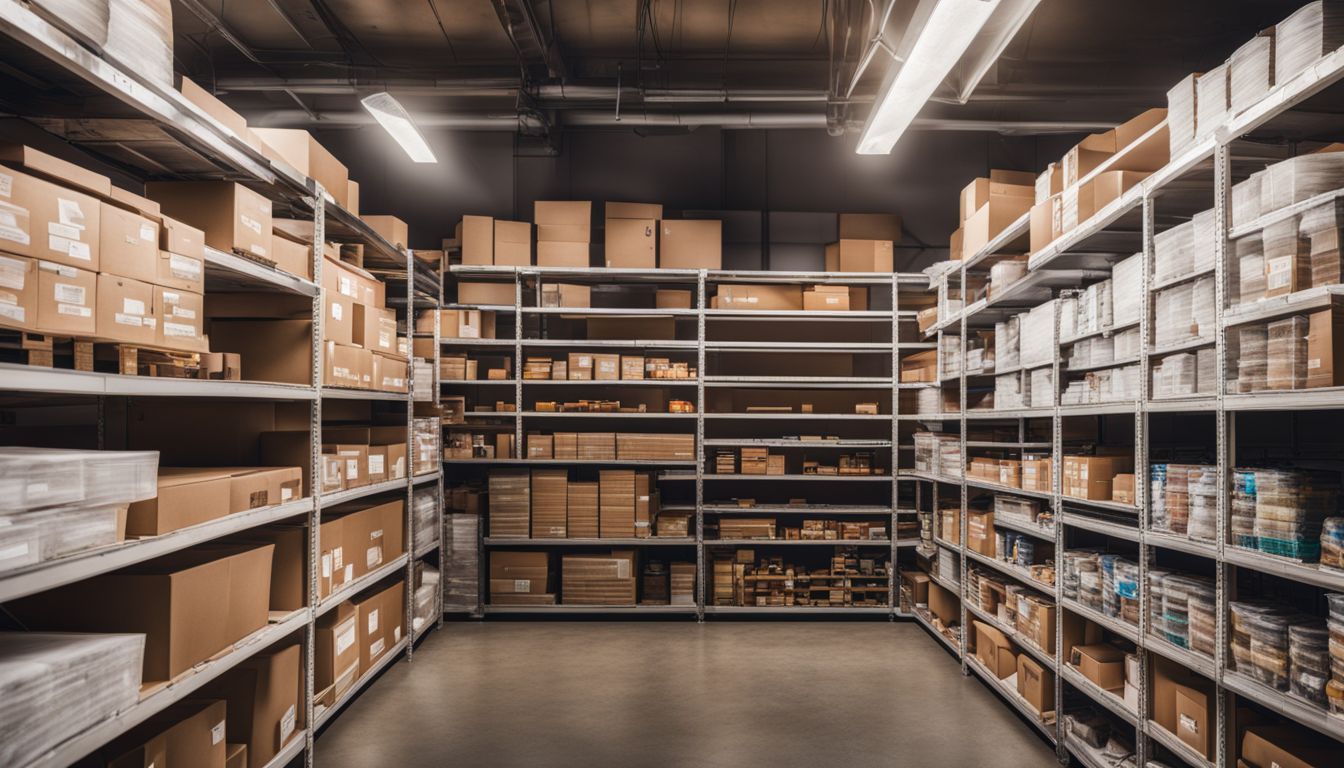
Maintaining minimum stock levels offers several benefits for businesses. Firstly, it helps prevent stockouts and ensures that customers can always find the products they need. This leads to fewer missed sales opportunities and keeps customers satisfied.
Secondly, having an optimal inventory level reduces the amount of money tied up in storage costs. By keeping inventory levels low but sufficient, businesses can avoid overstocking and make wise cash investments.
Lastly, minimum stock levels enable early detection of any issues in the supply chain or production process. By monitoring inventory closely, businesses can identify potential problems such as supplier delays or unexpected spikes in demand.
This allows them to take proactive measures to address these issues before they impact customer satisfaction or profitability.
Overall, maintaining minimum stock levels is essential for ensuring smooth operations, maximizing customer satisfaction, and optimizing financial resources in a business setting.
Example: Calculating Minimum Stock Level for Your Online T-shirt Store
Setting the minimum stock level for your products is a crucial step in inventory management. Let's walk through an example using an online clothing store that sells t-shirts to illustrate how you can calculate the minimum stock level effectively.
Step 1: Determine Production and Order-Fulfillment Times
- Production Time: Find out how long it takes to produce a new batch of t-shirts. In this example, let's assume it takes 2 weeks for your supplier to manufacture and deliver a fresh batch of t-shirts.
- Order-Fulfillment Time: Determine the average time it takes to fulfill an order and deliver it to your customers. For instance, let's say it takes 3 days from the moment a customer places an order to when the t-shirt is delivered.
Step 2: Estimate Maximum Customer Demand
- Historical Sales Data: Analyze your historical sales data to identify the maximum number of t-shirts that customers typically buy in a given period. In this scenario, you discover that the maximum demand is 20 shirts per week.
Step 3: Create the Minimum Stock Level Formula
Now, let's use these numbers to create a formula for calculating your minimum stock level. In this example, we'll use the average demand method:
- Minimum Stock Level Formula: (Production Time + Order-Fulfillment Time) x Maximum Customer Demand = Minimum Stock Level
Step 4: Calculate the Minimum Stock Level
Putting the formula into action:
- Minimum Stock Level Calculation: (2 weeks + 3 days) x 20 shirts = 46 shirts
So, in this case, you would need to maintain a minimum stock level of 46 shirts at all times to meet customer demand without running out.
This example demonstrates one way to calculate the minimum stock level, specifically using the average demand method. Remember that this method can be adjusted to suit your unique business circumstances and should be periodically reviewed and updated to adapt to changing market conditions and customer behaviors.
FAQs about Minimum Stock Level
What is the formula for reorder level?
The formula for calculating the reorder level is a combination of factors that help determine when to place new orders for inventory. It considers the lead time, which is how long it takes to fulfill and deliver an order, along with the average daily demand or sales.
Safety stock is also taken into account - this is extra inventory kept as a buffer against unexpected events like increased demand or delays from suppliers. By multiplying the average daily demand by the lead time and adding the safety stock, businesses can calculate their reorder level and know when it's time to replenish their inventory.
This helps ensure there are no stockouts or missed sales due to insufficient stock on hand. Automating this calculation through an inventory management system can make it easier for businesses to maintain optimal levels of inventory for efficient operations.
What are stock levels?
Stock levels refer to the quantity of a product or item that is currently available in inventory. It represents how much stock is on hand at any given time. Stock levels are important because they determine whether a business has enough products to meet customer demand or if there is a risk of running out of stock.
By monitoring and managing stock levels effectively, businesses can avoid stock-outs and ensure that they have enough inventory to fulfill orders in a timely manner. Calculating minimum stock levels helps businesses maintain adequate inventory while also minimizing storage costs.
Is safety stock necessary for all companies?
Safety stock is necessary for all companies to prevent stockouts and delays in order fulfillment. It acts as a buffer, ensuring that there is enough inventory available when unexpected spikes in demand or supplier delays occur.
Without safety stock, companies risk losing sales and damaging their reputation. By maintaining an adequate level of safety stock, businesses can mitigate the impact of uncertainties in the supply chain and ensure uninterrupted operations.
Clear communication with manufacturers regarding inventory needs is crucial for managing safety stock effectively and avoiding costly disruptions in the production process.
What is the difference between safety stock and minimum stock?
Safety stock and minimum stock are both important concepts in inventory management, but they serve different purposes. Safety stock is the extra inventory held as a buffer to protect against unexpected fluctuations in demand or supply, while minimum stock refers to the lowest level of inventory that a business should maintain to ensure continuity of operations and prevent stockouts.
In other words, safety stock accounts for variability in demand and supply, whereas minimum stock is the baseline inventory level needed to keep things running smoothly. Safety stock is typically higher than minimum stock because it takes into account factors like supplier delays or unexpected spikes in demand.
Calculating these levels accurately is crucial in order to avoid running out of stock and save money on storage costs.
3 Big Tips for Maintaining Optimal Inventory Levels
1. Conduct Regular Inventory Audits
Regular inventory audits are an essential practice for maintaining optimal inventory levels. By conducting these audits, businesses can ensure that they have the right amount of stock on hand to meet customer demand without overstocking.
Regular audits help in identifying any discrepancies or inaccuracies in the inventory records, allowing for timely adjustments and preventing stockouts. It also helps in saving costs by reducing storage expenses and minimizing the risk of obsolete inventory.
SkuVault is an inventory management solution that automates tracking of inventory metrics, making it easier to conduct regular audits and maintain accurate stock levels. Businesses, especially direct-to-consumer brands, can streamline their inventory management practices and improve overall business performance by implementing regular audit processes.
2. Reduce Lead Times
Reducing lead times is a crucial step in maintaining optimal inventory levels. Lead time refers to the time it takes for an order to be fulfilled from the moment it is placed. By reducing lead times, businesses can ensure that products are readily available and avoid stockouts or delays in order fulfillment.
This can be achieved by improving communication with suppliers, streamlining production processes, and utilizing technology to track and manage inventory efficiently. By minimizing lead times, businesses can meet customer demand quickly and reduce the risk of lost sales or dissatisfied customers.
3. Use an Inventory Tracking System
An inventory tracking system is a valuable tool for managing and monitoring your stock levels. It allows you to keep track of your inventory in real-time, providing you with accurate information about what products are available and how much of each item you have on hand.
By using an inventory tracking system, you can reduce total inventory costs by 10 percent and improve your overall inventory control. This system provides you with visibility into stock levels, allowing you to make informed decisions about when to reorder items and avoid overstocking or running out of important products.
With real-time access to stock levels, you can optimize your order quantities, streamline your supply chain processes, and ensure that you always have the right amount of stock on hand to meet customer demand.
Conclusion
In conclusion, calculating minimum stock levels is crucial for businesses to avoid stock-outs and manage inventory efficiently. By using methods such as the Average Demand, Safety Stock, and Reorder Point methods, businesses can ensure that they always have enough stock on hand to meet customer demand without overstocking.
Implementing these calculations and maintaining optimal inventory levels will help businesses achieve better cash flow, reduce costs associated with stockouts or excess inventory, and improve overall efficiency in their supply chain operations.
Don't underestimate the power of accurate inventory management - it can make a significant impact on your business's success!
Additional FAQs
1. What is the minimum stock level formula?
The minimum stock level formula makes use of normal consumption, delivery time, and extra demand during lead time to figure out the smallest amount of inventory your business needs.
2. How can I manage my eCommerce inventory better?
You can improve your eCommerce inventory by using an inventory management system (IMS) or ops optimization tool like Cogsy. These tools send automated reorder point alerts and help maintain healthy liquidity ratios.
3. Why is it vital to study maximum and minimum consumption rates?
Knowing about your product's maximum and minimum consumption rates helps set accurate reordering levels for peak profitability while avoiding issues like backordering and high overhead costs.
4. What are some risks in managing a warehouse's minimum stock levels?
Some risks include having too much working capital tied up in unused items, higher holding costs due to excess products, running out of popular items, increasing freight costs from rush reorders.
5. Can China sourcing agents aid me with maintaining supply chain efficiency?
Yes, a good China sourcing agent will ease the process of product sourcing and supplier negotiation, offer support for quality control plus manage warehouse preparation, shipping & delivery times lowering e-commerce supply chain stressors.
6.How important is understanding customer demand in calculating Minimum Stock Levels?
Understanding customer demands plays a key role; knowing sales forecasts allows you to determine accurately when low-stock alerts should be triggered for replenishing stocks ensuring continuous production fulfilling market trends.