-ceb73ad5fd-3912938455.jpeg)
Facing challenges in managing your inventory can be quite a headache for businesses. Did you know, Weeks of Supply (WOS) is an incredibly useful tool that helps estimate how long your current stock will last? Our blog will divulge the secrets on how to effectively calculate WOS and implement it for improved inventory management.
Continue reading, discover something new, and say goodbye to those pesky inventory woes!
Understanding Weeks of Supply (WOS)
-d152122c0a-598922509.jpeg)
Weeks of Supply (WoS) is a metric that measures how long your current inventory levels are expected to last based on your historical or projected sales rate. It helps e-commerce businesses assess their inventory turnover and make informed decisions about restocking, purchasing, and managing stock levels.
The formula to calculate Weeks of Supply is:
WoS = (Total Inventory Quantity) / (Average Weekly Sales)
Essentially WOS tells you how long your current stock will last in terms of weeks. Typically a business will use past sales data to calculate WoS. Businesses find aWeeks of Supply (WoS) handy when they don't want to run out of items or tie up too much money in stuff that just sits on a shelf.
Getting the WOS right is crucial for all retailers and even manufacturers. For them, knowing their Weeks of Supply can stop things like dead stock and spoilage making problems down the line.
Having good control over this also means not losing sales due to no stock being available. When used along with other tools such as SOS Inventory, it can prove very effective for maintaining inventory health.
Importance of Accurately Calculating Weeks of Supply
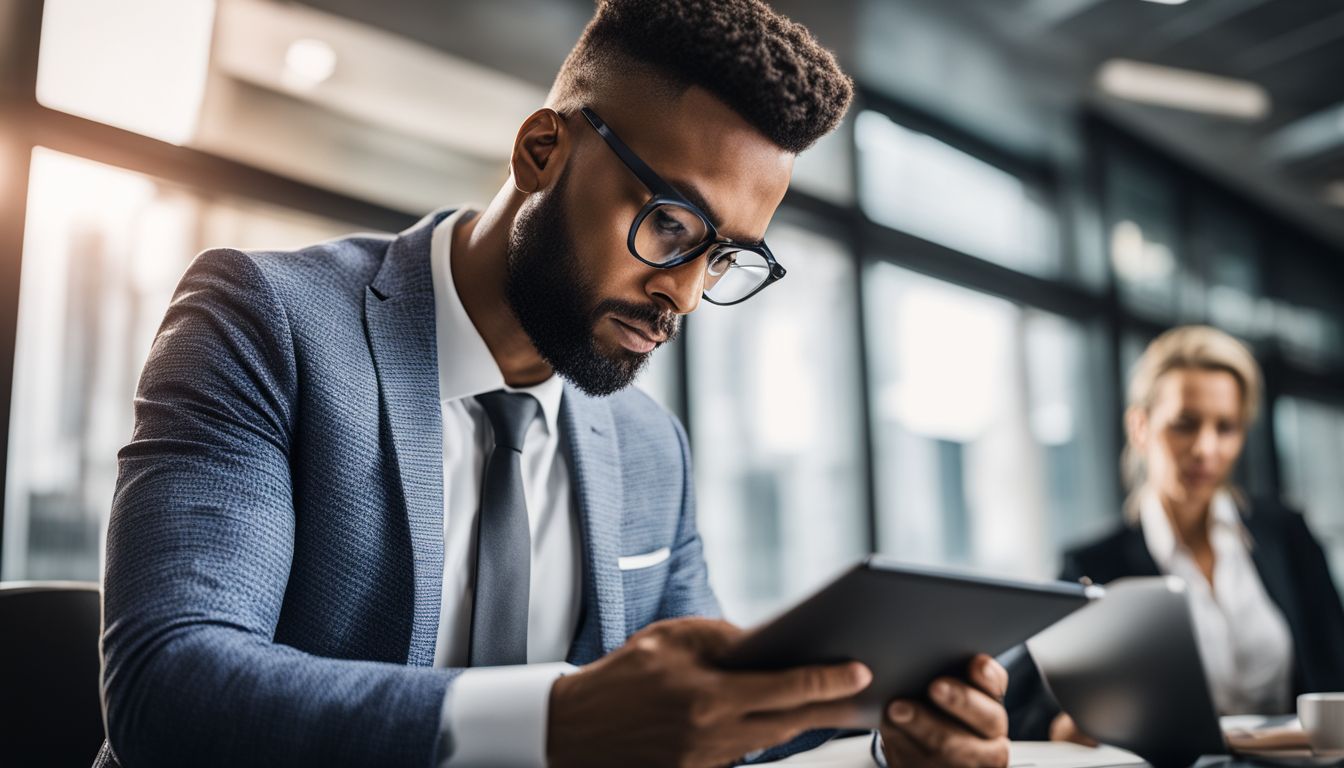
Accurately calculating weeks of supply (WOS) in inventory management significantly elevates your business operations. It enables strategic forecasting for demand and seasonality, establishes dynamic relationships with suppliers, ensures optimal financial planning, enhances the efficiency of your supply chain processes and keeps your stock levels well-balanced between excesses and shortages.
By having a precise WOS calculation, you ensure a smoother product flow that resonates with customer expectations while maintaining operational cost-effectiveness.
Better Inventory Management
Keeping the right amount of stock makes your business run smooth. The Weeks of Supply (WOS) can help with this. By using WOS, you know how much inventory to have on hand for each product.
You will avoid having too much or not enough.
Using tools like Cogsy and real-time inventory management helps track your goods better. This gives you an up-to-the-minute look at what is hot and what's not in your store! With this info, you can order more of what sells fast and less of slow items.
Avoiding Stock Outs
Running out of goods is bad for your business. Weeks of Supply (WOS) helps to stop this from happening. Stock outs can make you lose sales and disappoint customers. With a good WOS, you will know when to order more goods before they run out.
You need to look at how fast items sell and how long it takes new stock to get here. This way, you keep enough goods in store at all times.
Minimizing Excess Inventory
Too much stock can cost a lot of money. We call this "excess inventory." It sits on shelves, takes up space and does not earn any money. Excess inventory causes spoiled goods and dead stock for many businesses too.
But there is a way to keep the right amount of supply – with Weeks of Supply (WOS)! WOS tells how long your current supply will last based on past sales. This way you buy only what you need, when you need it! Goodbye to crowded shelves and wasted cash! Minimizing excess stock makes better use of work funds tied up in stored items.
Your business saves more money this way.
Improved Supply Chain Efficiency
Having a good WOS count helps the supply chain run better. This is because it leads to fewer stockouts and excess inventory. The team knows when more goods should come in. They can plan for them so that they fit into the process with no problems.
Businesses also cut down on costs and use less space for storage. With all these, customer relationships get stronger as products are always available when needed.
Enhanced Financial Planning
Good financial planning needs the right data. One great tool is Weeks of Supply (WOS). It can help a company plan for costs up ahead. Correct WOS figures play a strong role in having just enough stock.
This helps reduce inventory holding costs and spoilage. At the same time, it keeps customers happy by making sure products are always ready to sell. All this leads to better use of working capital, cutting down on waste and saving money! To get accurate WOS numbers, though, quality data inputs are vital - no guess work here! With good info going in, you also have useful insights coming out that guide your Purchasing decisions later on.
Demand and Seasonality Analysis
Sales can change with the seasons. This is known as seasonality. For example, warm clothes sell more in winter than in summer. Understanding this helps plan inventory better.
Weeks of Supply (WOS) uses this understanding. It looks at past sales to know how it changes through the year. This can help forecast future demand and manage stock better.
Strengthened Supplier Relationships
Good supplier ties can guide your store to big wins. Calculating Weeks of Supply (WOS) often gives suppliers a clear picture of what you want. This helps both sides avoid surprise orders or mix-ups.
As trust grows, suppliers may offer better deals or faster ship times to you. In turn, your stock comes in on time and keeps customers happy. Strong links with suppliers also help when there's a slip-up like late shipments or missing items.
With a bond in place already, it's easier for both sides to fix problems fast and move forward again.
The Formulas to Calculate Weeks of Supply
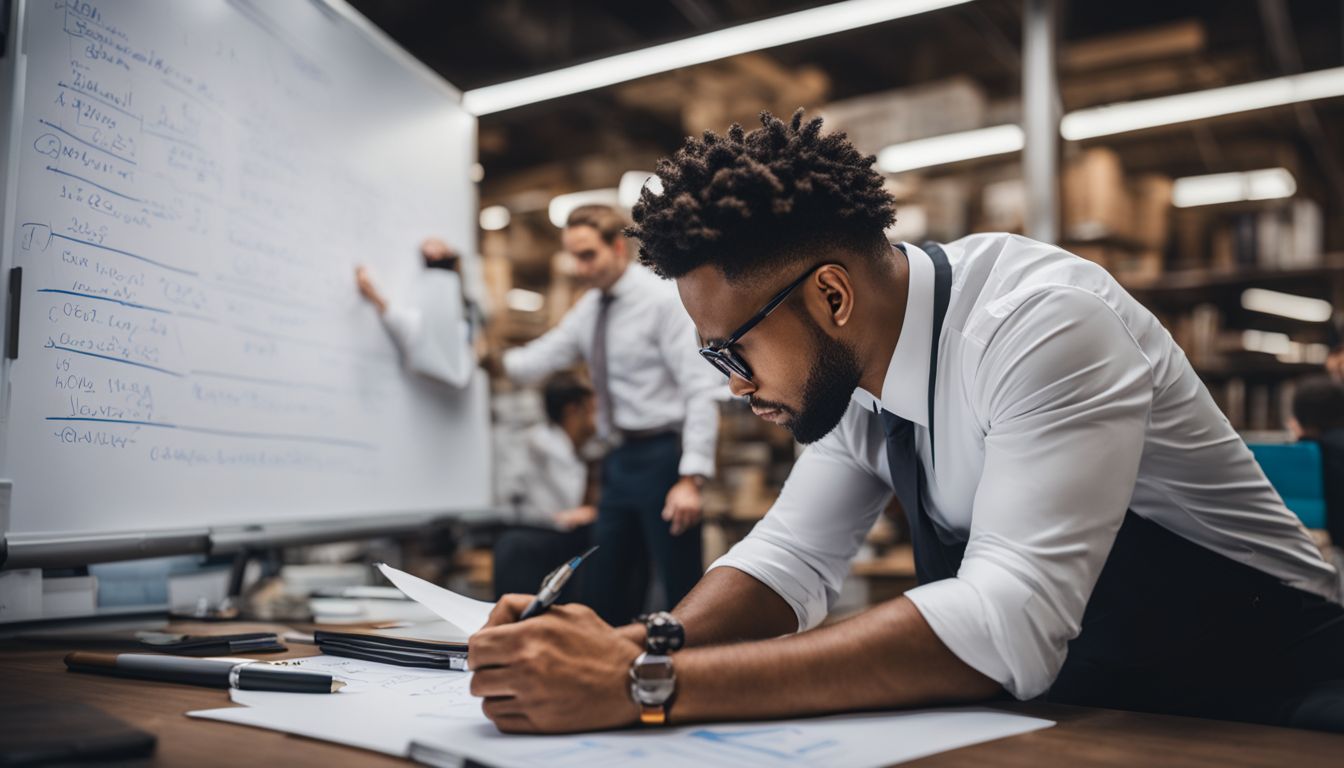
Understanding how to calculate Weeks of Supply is crucial for effective inventory management. The most common formula takes your current stock level and divides it by the average sales per week.
For a more forward-thinking approach, many businesses also use the Forward Weeks of Supply (FWOS) formula - this involves dividing future planned stocks by forecasted demand for that period.
Weeks of supply formula
The weeks of supply formula is a tool. It tells us how long our current stock will last. This count starts from today and goes on until the day we run out of items to sell. To find this out, we divide our total inventory by the weekly sales rate.
But here's more good news! With this formula you can plan better for your business needs. For example, you might weed out slow-selling goods or invest more in top performers. Not just that, but also plan ahead for busy seasons and market changes.
So never underestimate the power of a well-known number like 'weeks of supply’!
Forward weeks of supply (FWOS) formula
The FWOS formula tells you how long your stock will last. You use it when you know future needs for goods, not past sales. The math is simple: Divide the goods on hand by forecasted weekly demand.
Your answer shows how many weeks your current supply will last based on what people might buy in the future. The FWOS formula helps to avoid running out of items or keeping too much stock.
It uses both real-time inventory management and forecasted demand data to give a clear picture of inventory health.
Potential Limitations of the WOS Calculation
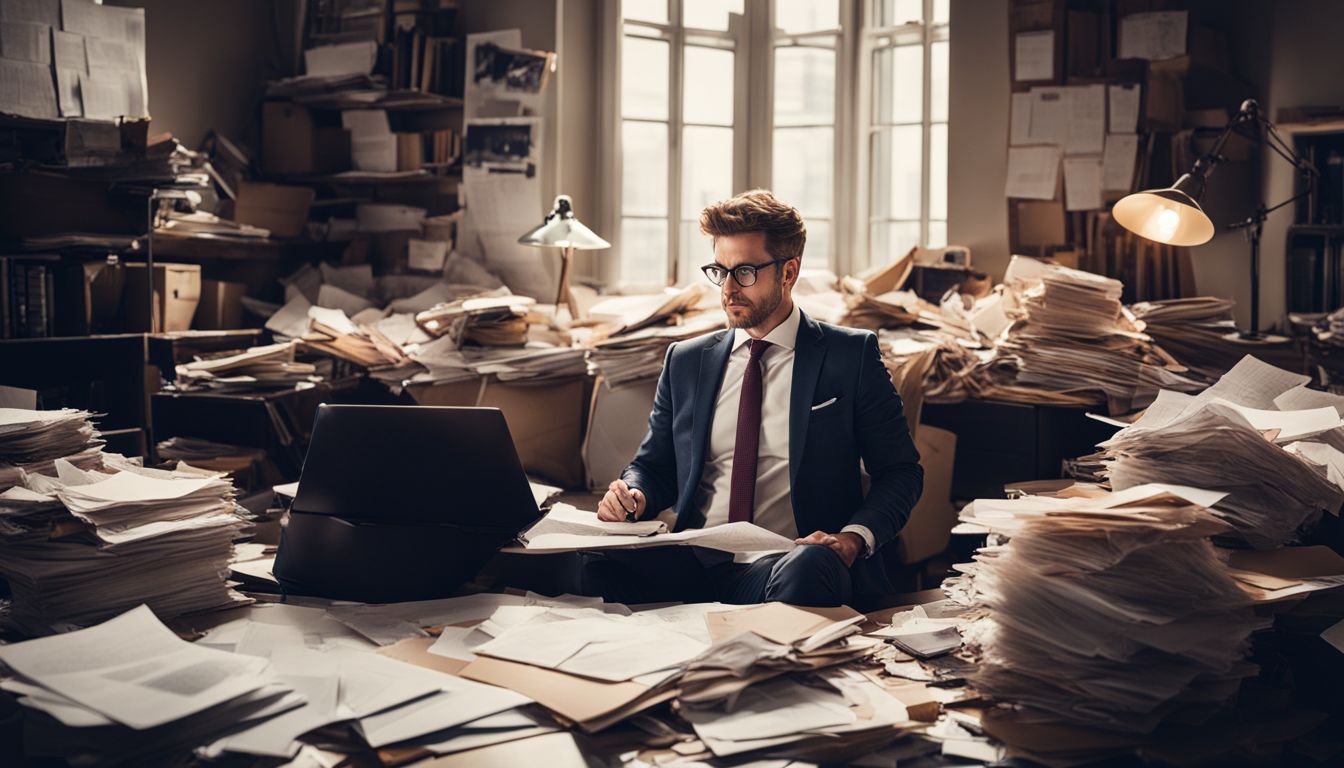
While WOS calculation can provide useful insights for inventory management, it’s important to understand its limitations. Dependence on insufficient data is one critical obstacle; if there isn't enough accurate data to calculate WOS, the results might not be beneficial.
Another limitation arises from focusing only on past trends which may ignore the potential impact of future market changes or unforeseen circumstances. Ignoring seasonality while calculating WOS could lead to overstocking during off-peak seasons and understocking during peak demand periods.
Overlooking sales trends is another area of concern as sudden surges or drops in sales can dramatically alter supply requirements. Additionally, the quality of data outputs heavily influences your analysis; low-quality data will likely yield unreliable outcomes.
Understanding these potential pitfalls allows businesses to use weeks of supply more effectively in their overall inventory strategy.
Dependence on insufficient data
Not having enough data can be a big problem. This might happen when you are new in the business world or don't track your sales well. Your Weeks of Supply (WOS) calculations could be off if your data is not good.
You might order too much stock or not enough if you get it wrong. It's very important to keep all your numbers correct and up-to-date so that this does not happen.
Focusing only on past trends
Just using old trends can hurt. It does not always show what will happen next. For example, last year's best-selling toy might not sell well this year. This could lead to too much stock and money loss.
Sales can change fast. New products or a sudden jump in demand can shake things up. These changes do not appear when one only looks at past sales data.
Ignoring seasonality
Some goods sell more at certain times of the year. This is called seasonality. If you ignore these changes, it can mess up your Weeks of Supply (WOS) count. Examples are toys during Christmas or swimwear in the summer.
Failing to account for this might lead to having too much or too little stock which hurts business and waste space and money.
Overlooking sales trends
Sales trends are vital in business. Failing to watch these can lead to problems with stock levels. If sales are up, you might not have enough goods on hand. If sales fall, you could end up with too much stuff.
This can mean more waste and lost money. Paying close attention to what sells well and when can help your business adapt as needed for success.
Quality of data outputs
Good data makes good plans. For Weeks of Supply (WOS) you need the best data. This means clear, exact and up-to-date facts. Errors in your data can lead to bad results with WOS counts.
Poor quality outputs may also cloud your view of inventory needs. Say no to wrong, slow or stale data if you want accurate supply timetable calculations!
5 Tips for Optimizing Weeks of Supply & Inventory Replenishment
Implementing strategies to optimize your weeks of supply and inventory replenishment can significantly improve your business operations. Keep a tight rein on minimum order quantities (MOQ) to avoid overstock.
Regular analysis of performance and stock helps identify trends paving way for proactive decisions. As consumer demands fluctuate with seasons, accurate forecasting keeps you prepared for these variations.
Maintaining strong supplier relationships ensures consistent supply essential in predictable inventory management. Stay alert about supply variability due to unexpected scenarios like supply chain issues or sudden increase in demand for effective mitigation.
1. Keeping on top of minimum order quantities (MOQ)
You need to watch the minimum order quantities (MOQ) from your suppliers. Suppliers set these MOQs to make sure making and sending goods is worth their time and money. But if you order too much, you may have too much stock.
That means tying up your cash in items sitting on the shelf. To avoid this, hold regular stock audits. You can find room for better deals with audits. Technology tools like Cogsy can help too by working out changing market trends into your plans for managing stocks and setting MOQs.
2. Regularly analyzing performance and stock
Don't let stock sit too long. Look at it often. Count what you have and see how fast it sells. This can help you know when to order more things. You don't want to run out of stuff that sells fast.
But you also do not want a lot of things that no one buys.
3. Forecasting seasonal fluctuations
Seasons change and so do sales. It is key to guess these changes in demand before they happen. This guessing game is called forecasting seasonal fluctuations. For example, a toy store may sell more toys during the holiday season.
A swimsuit shop may see high sales in the summer months but not much in winter. Using past sale data can help figure out these patterns of ups and downs in sales tied to seasons or events.
Then you can plan your inventory better using Weeks of Supply (WOS). By doing this well, no product will sit too long on shelves or run out before more inventory arrives.
4. Maintaining strong supplier relationships
Having good ties with suppliers is key. These relationships help a firm serve their customers better and manage stock more efficiently. Trust and open talk with suppliers can make teamwork better.
This trust helps in solving problems.
Being friends with your suppliers can give your business new chances to grow. A strong bond with a supplier is needed for steady supplies of goods. In the end, it will keep the supply chain working safely and on time.
5. Staying on top of supply variability
Changes in supply can happen fast. This is known as supply variability. It's key to keep track of this and make smart plans. For example, if there are delays, you need more stock to meet demand.
If supply comes in too early, you might end up with too much inventory on your hands which costs money to hold onto. So, keeping a close eye on changes in your supply chain makes sure that it all runs smooth and reduces nasty surprises!
Conclusion
So, you see how simple it is to calculate weeks of supply (WOS)? It helps keep your stock just right. No more stress about having too much or not enough goods to sell. Start doing your WOS count now for a smooth running business!
Key Takeaways
- Weeks of Supply (WOS) tells us how long our stock will last. It uses past sales data.
- A good WOS count helps a business run better. We can avoid problems like having too much stuff or running out of goods to sell.
- To find the weeks of supply, we divide total inventory by weekly sales rate.
- The Forward Weeks of Supply formula also helps us plan for future needs. With this formula we divide items on hand by predicted weekly demand.
- If there is not enough correct data, it can mess up our WOS counts. So keeping all numbers right and fresh is very important!
- Always watch changes in what sells well and when they do so! This helps keep stock levels at their best range while saving money and space for your business!
FAQs
1. What is Weeks of Supply (WOS) and how do we calculate it?
Weeks of Supply (WOS) tells us how long our current stock will last at the present sales rate. We find WOS by dividing on-hand inventory by the average weekly consumption rate.
2. How can I use WOS in my inventory planning?
Inventory planning with weeks of supply helps to manage optimal order quantities to meet demand forecasts, while also considering supplier lead times and seasonal products.
3. Can using an Excel spreadsheet or Inventory Software help me manage my WOS better?
Yes! Tools like Excel spreadsheets or Inventory Software are ideal for tracking your WOS data accurately and maintaining good inventory visibility.
4. Why is accounting for backorders important when calculating Weeks of Supply?
Backorders show that you don't have enough goods in stock to fill requests right away, this might mean your weeks of supply need to increase so you can fulfill future orders faster.
5. Is knowledge about Planned receipts vital when dealing with Weeks Of Supply calculation?
Absolutely! Knowing planned receipts gives insights into incoming stocks which aids in managing your replenishment strategy based on demand forecasting effectively.
6. Do factors such as marketing events and demands fluctuations impact the calculation of Weeks Of Supply?
Yes, they do! Instances like viral posts from marketing campaigns causing a spike in consumer demand should be factored into recalculating weeks of supply metric accordingly.