Understanding The Forward Stock Cover Formula: Calculation And Application In Inventory Management
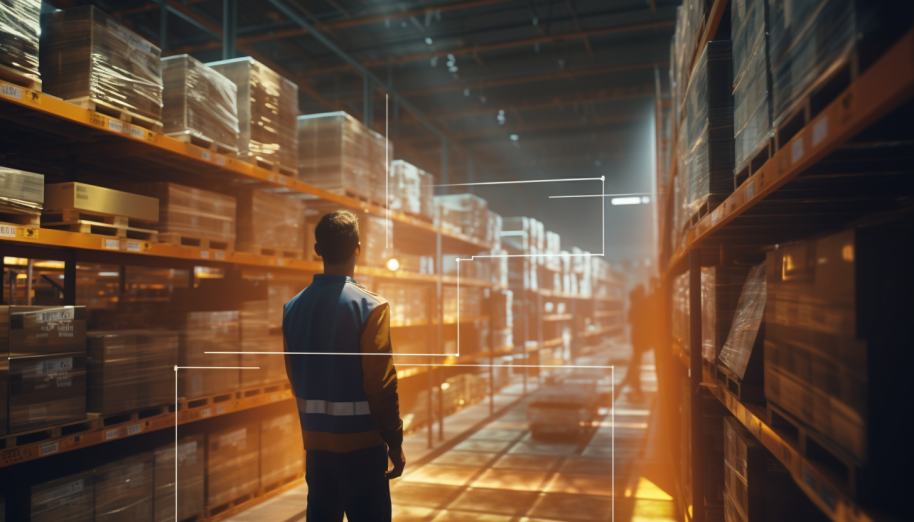
Are you grappling with the challenges of managing your inventory and determining the right stock levels to maintain? Enter the world of stock coverage, a critical component in the realm of inventory management. This article delves deep into the forward stock cover formula, walking you through its calculation, and demonstrating its practical application in optimizing your business inventory. Buckle up for a journey that will revolutionize your warehouse operations!
Key Takeaways From This Article
- Stock coverage is a measure of how long existing inventory will last based on average sales.
- The stock coverage formula is calculated by dividing the current inventory by the average demand or sales.
- Understanding stock coverage helps businesses avoid overstocking or running out of goods, saving money and meeting customer demand.
- Inventory software plays a crucial role in managing stock coverage, automating calculations and providing real-time information on stock status.
Understanding Stock Coverage
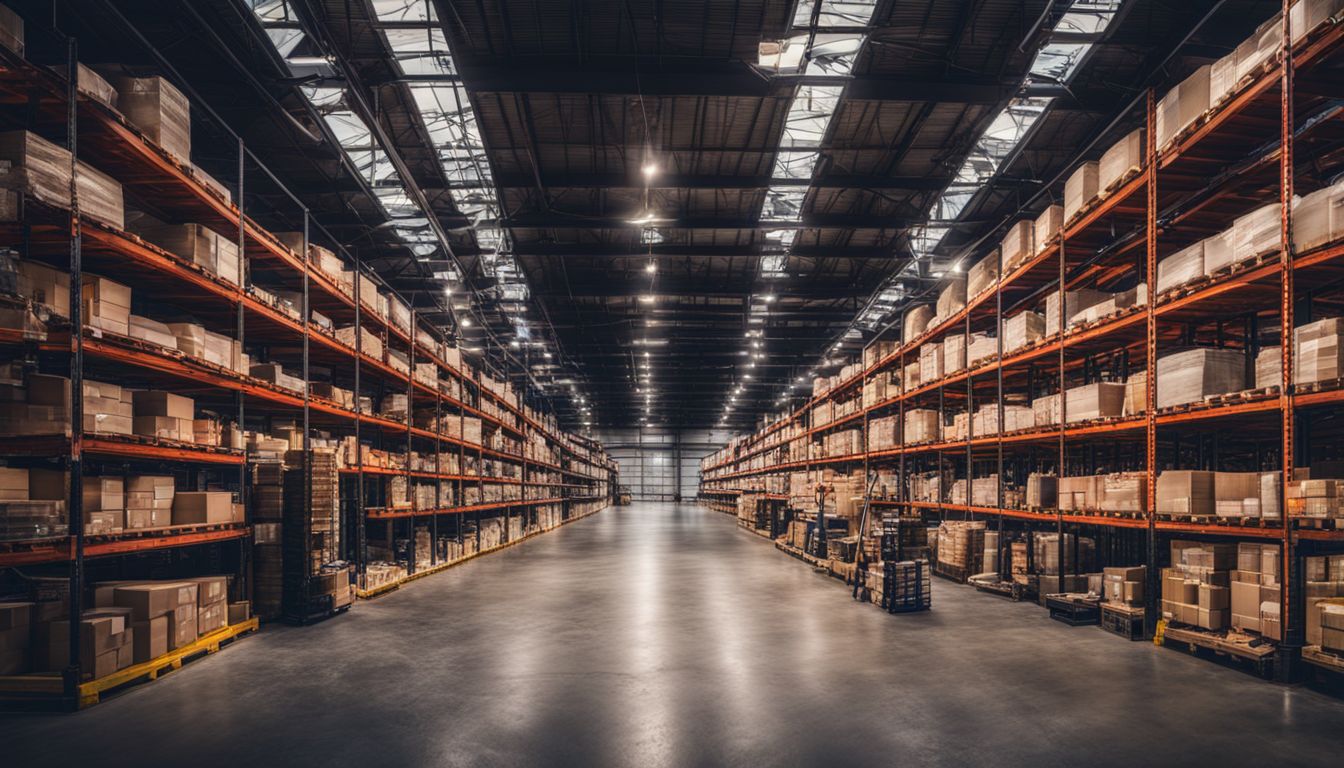
Stock coverage is a crucial logistics metric that measures the number of days an inventory can meet customer orders without stockouts, making it essential for effective inventory management.
What is Stock Coverage?
Stock coverage, a pivotal logistics metric, tells you how many days your inventory can satisfy customer orders without running out, making it indispensable for effective inventory management.
What is Stock Coverage?
Picture this: Stock coverage reveals the number of days your company can sell goods without facing stockouts. It's the duration, in days, during which your firm can fulfill customer demands using its current stock. Managers wield this metric as a crystal ball to plan new orders and streamline their warehouse operations.
Stock coverage is computed by dividing the stock you have on hand by the average sales within a specific timeframe. Keeping a vigilant eye on stock coverage can make or break your inventory management game.
How is Stock Coverage Calculated?
Let's break down the math behind stock coverage in simple steps:
- Find Your Current Inventory: Begin by tallying up the total quantity of goods in your warehouse. This is your current inventory.
- Determine Average Demand or Sales: Next, unearth the average demand or sales figure. Reviewing past records is a smart way to nail this number.
- Divide to Conquer: Divide your current stock volume by the average demand. This equation yields the coverage period, indicating how long your current goods will last.
Regularly revisiting this calculation is your ticket to averting stockouts and economizing on storage costs.
Forward Stock Cover Formula: A Detailed Look
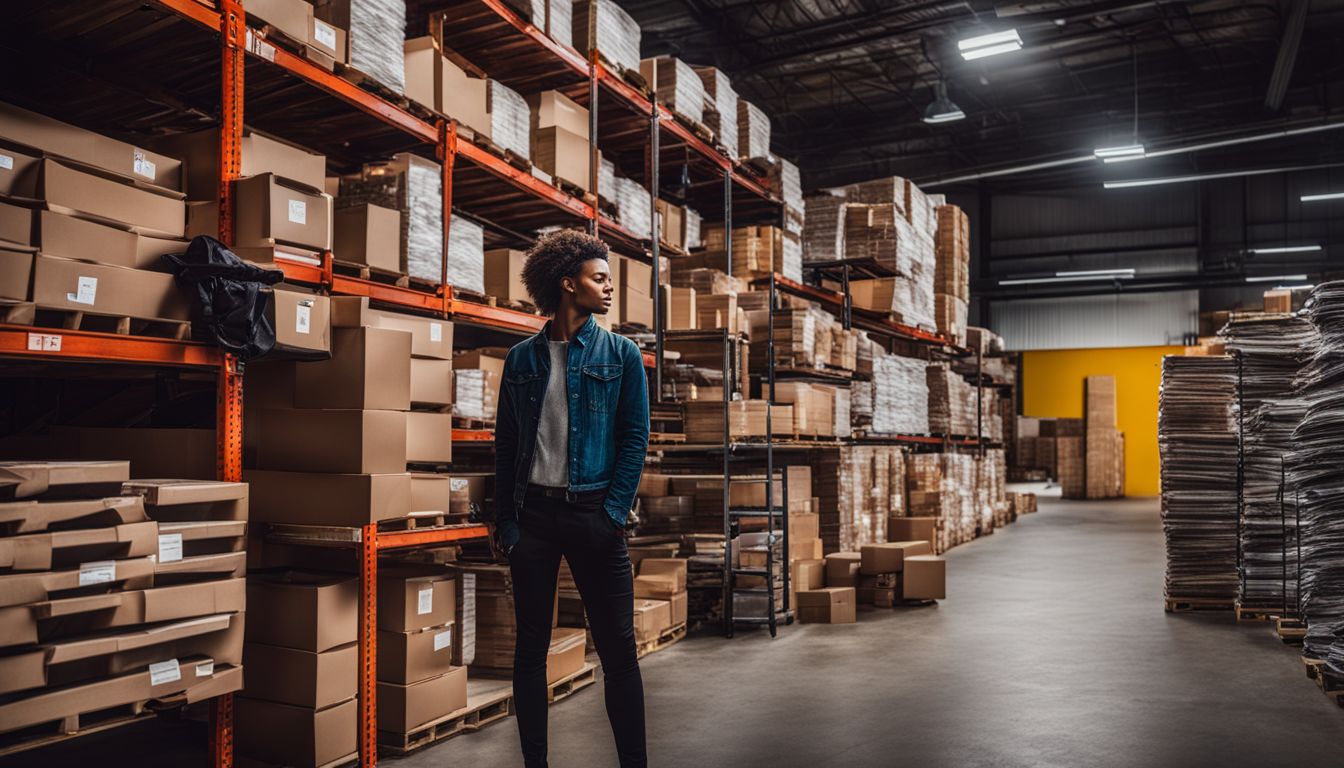
The forward stock cover formula offers a detailed calculation that empowers you to assess inventory availability and make informed decisions in the realm of inventory management.
Explanation and Calculation
Let's demystify the mathematics of stock coverage. Imagine you're running a store stocked with 500 items. Over the span of a week, you consistently sell around 100 items. To calculate your stock coverage, simply divide your stock quantity (500) by the average sales (100). The result? Five weeks of stock coverage, assuming sales remain constant.
Practical Application in Inventory Management
Inventory managers employ the forward stock cover formula in their daily routines. This tool helps them gauge how many days their current stock will last, contingent upon the rate at which items are flying off the shelves.
This formula serves as the guardian against overstocking, which incurs excessive storage costs, and low stock levels, which lead to missed sales opportunities. Moreover, savvy managers use this calculation to time their orders perfectly, ensuring new goods arrive just as the old ones are depleting.
The role of a Warehouse Management System (WMS) is pivotal here, providing real-time intel on what's in stock, what's selling like hotcakes, and what needs reordering pronto.
Interpreting Stock Coverage
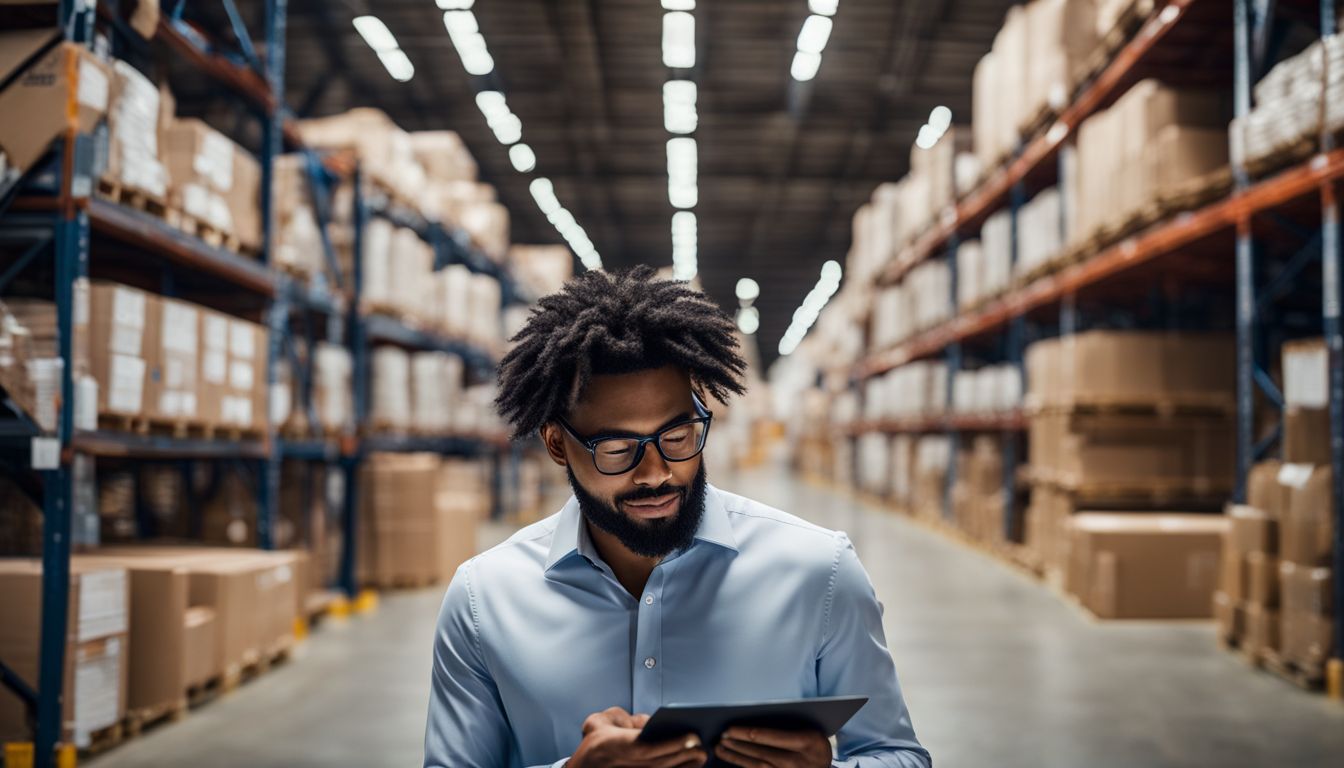
Mastering stock coverage entails not only calculating it but also leveraging the results for effective inventory management.
Understanding Results
Stock coverage is a crucial metric in inventory management that helps businesses understand their ability to meet customer demand. When interpreting stock coverage results, it is important to remember that a high ratio indicates a longer period of time during which customer orders can be fulfilled with existing inventory.
On the other hand, a low stock coverage ratio suggests that there may be a higher risk of stockouts and being unable to meet customer demands. By analyzing these results, businesses can make effective decisions regarding their stock levels and take action to optimize inventory availability and avoid potential disruptions in supply chain operations.
Making Effective Decisions Based on Outcomes
- Analyze the stock coverage results to identify any issues or opportunities for improvement.
- Determine if the current stock coverage meets the desired target or if adjustments are needed.
- Assess the impact of changing variables, such as average sales or supplier lead time, on stock coverage.
- Consider the financial implications of stock coverage, such as storage costs and potential lost sales due to stockouts.
- Use data analytics and business intelligence solutions to gain insights into inventory performance and make data-driven decisions.
- Take into account factors like seasonal influences on product sales and new product launches when evaluating stock coverage.
- Address any excess or obsolete stock identified through the analysis of stock coverage.
- Continuously monitor and adjust stock levels based on changes in demand, supplier orders, and customer preferences.
Role of Inventory Software in Managing Stock Coverage
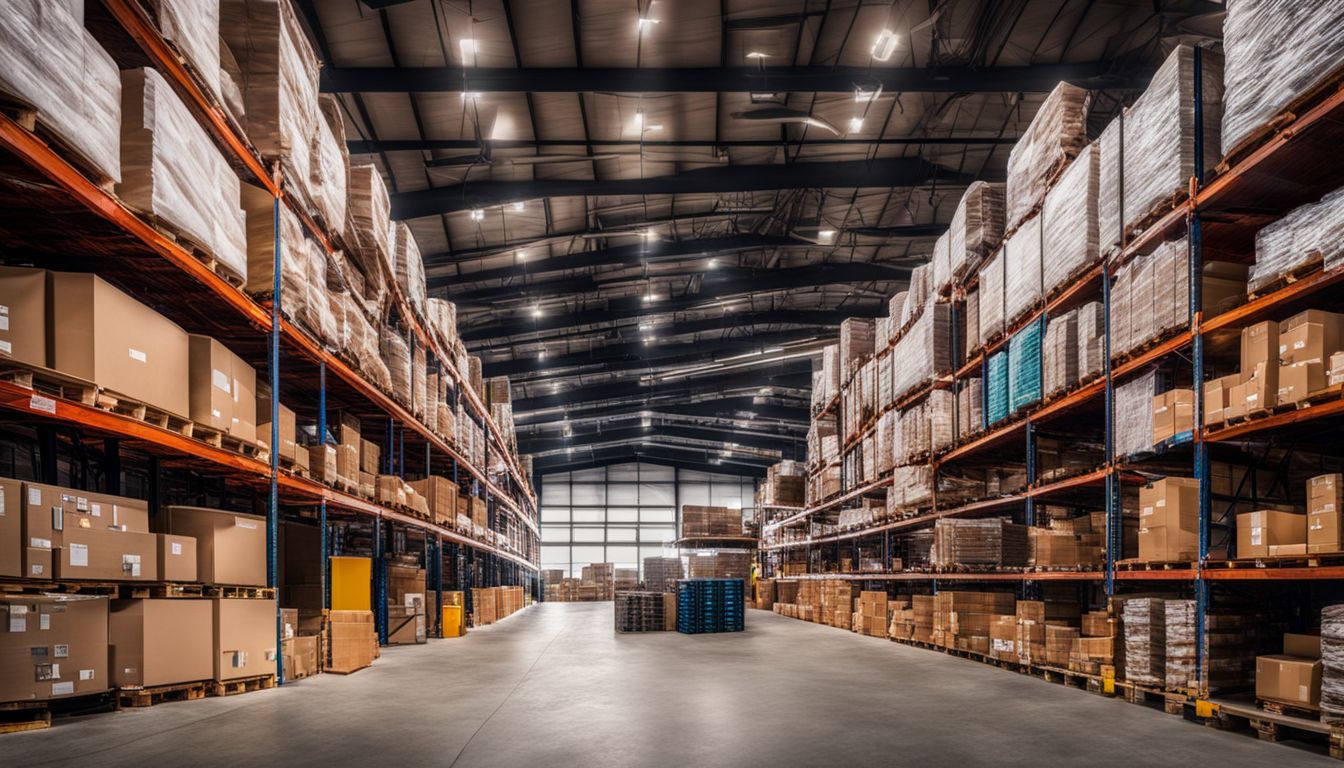
Inventory software plays a crucial role in managing stock coverage and improving inventory management efficiency. By automating the calculation of stock coverage, inventory software eliminates the need for manual calculations and reduces the chances of errors.
It provides real-time information on stock status and availability, allowing warehouse managers to make informed decisions about stock replenishment.
With inventory software, businesses can easily track their current inventory levels and compare them to average sales for a given period. This helps in determining how long their existing stock will last based on past sales patterns.
The software also allows businesses to set optimal stock levels using formulas like EOQ (Economic Order Quantity), ensuring that they have enough stock without excessive overstock or risk of running out.
By using inventory software, businesses can maintain high stock coverage ratios, which means they can maximize inventory availability without unnecessary replenishment. This reduces the risks associated with excess stock or low coverage periods such as increased storage costs or unfulfilled customer orders.
Overall, inventory software is an essential tool for efficient stock management by providing accurate data, automating calculations, and enabling proactive decision-making to optimize stock coverage.
Conclusion
In conclusion, understanding the forward stock cover formula is crucial for effective inventory management. By calculating stock coverage, businesses can make informed decisions about their inventory levels and optimize warehouse efficiency.
Implementing inventory software and utilizing data analytics can further enhance the accuracy of stock coverage calculations and improve overall inventory management practices. With this knowledge, companies can avoid stockouts, minimize storage costs, and meet customer demand while maintaining optimal stock levels.
FAQs
1. What is the Forward Stock Cover formula?
The forward stock cover formula is a maths rule used in inventory management. It helps figure out how long the current inventory will last based on average sales.
2. How can warehouse managers use this formula for their business?
Warehouse managers apply this formula to avoid running out of goods (stockouts). The aim is to keep optimal stock levels and meet customer orders timely, also reduce storage costs linked with excess or obsolete stock.
3. Can I use Microsoft Excel and other tools for inventory control?
Yes! You can apply Excel formulas along with other digital solutions like Inventory Software or Warehouse Management System (WMS) tools that automate inventory control and give real-time information about your stocks.
4. Does the Forward Stock Cover Formula apply only during normal periods?
No, it does not! Both seasonal influences on product sales and new product launches affect average demand, so these factors are taken into account when using the forwarding stock cover method in practice.
5. Why do we need such formulas in logistics history?
Logistics metrics like these have always been key performance indicators (KPIs). Trends from small data analyzed over time became big data applied to more complex logistics scenarios for better decision making around order fulfillment, throughput efficiency, etc., thanks to Industry 4.0 advancements!
6. Are there any downside risks while using Forward Stock Cover calculations?
Misreading sales history might lead to either overstock creating dead stock quantities/slow-moving stocks, or understock leading to lost sales due to out-of-stock situations; hence accurate usage of this calculation matters.